First battery test laboratory with CO2-neutral refrigeration technology based on natural refrigerants
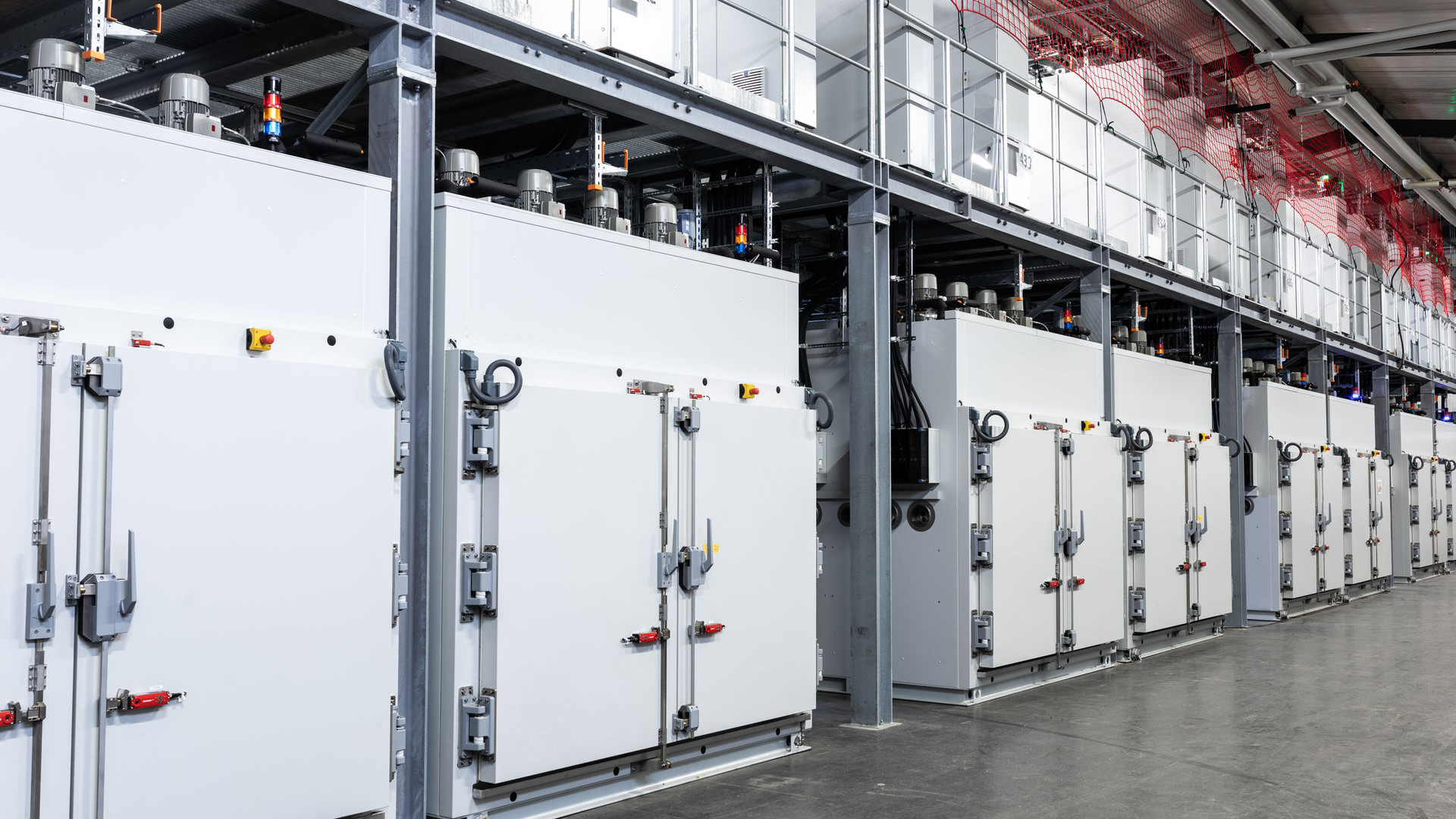
Batteries are the key components for electromobility and renewable energies. For a holistic, positive environmental balance, not only the battery technology itself, but also its development must become climate-neutral. This is where Voltavision, as a specialist in testing high-voltage batteries, has achieved another breakthrough with the first test laboratory with CO2-neutral refrigeration technology, in which CO2 and propane are used as refrigerants.
With several test laboratories with a total laboratory area of 4,600 square meters, 195 test chambers and 2111 test channels for cells, modules and batteries, Voltavision is one of the leading test service providers for high-voltage battery testing for vehicles in the development phase in Germany. As a pioneer in this field and a player in the transition to climate-friendly electromobility, Voltavision is constantly striving to work in the most climate-neutral way possible.
One challenge here was the refrigerants required. They are partially halogenated hydrofluorocarbons (HFCs) - which in turn are greenhouse gases and can damage the ozone layer. Reducing them is also necessary due to EU requirements from the “F-Gas Regulation”. This provides for the phasing out of HFCs by 2030. Voltavision has already succeeded in completely replacing them while maintaining the quality and reliability of the refrigeration process.
GWP below 3 and ODP of 0
In order to reliably carry out the important tests on product properties at low temperatures down to -40 °C in the test laboratories, Voltavision has been using specially developed temperature control units with high performance and low environmental impact for some time. Now, with the support of refrigeration engineers from Frigotechnik, Voltavision engineers have achieved another breakthrough and designed a system that relies entirely on natural refrigerants. This puts them well ahead of the restrictions on the use of fluorinated refrigerants, which will be gradually introduced by the EU by 2030: the system achieves a GWP value (Global Warming Potential) of less than 3 and an ODP value (Ozone Depletion Potential) of 0 - in other words, unlike many other refrigerants, it is completely harmless to the ozone layer.
The new air conditioning and refrigeration systems were developed in parallel with the construction of the Riemke III test laboratory in Bochum. A central refrigeration system there now supplies eight modified Voltacoolers, the temperature control units developed by Voltavision and already in use for some time. They make it possible to test batteries and other HV components under a wide range of conditions by precisely adjusting temperature control circuits in the vehicle or provoking very high temperature gradients.
Julian Stentenbach, Managing Director of Voltavision: “When Voltavision was founded in 2011, we already had the vision of supplying our laboratories with centralized refrigeration technology. The advantages of efficiency and cost savings are obvious. But for a long time we were unable to convince the manufacturers of our idea. In the meantime, we have become a certified refrigeration company ourselves and have acquired the know-how to install such systems over the last few years according to the “learning by doing” principle. To make significant progress in climate protection, we have to overcome dogmatism and break new ground.”
Central refrigeration system with propane operation
The new system has a cooling capacity of 2 x 190 kW at an evaporation temperature of -20 °C and was specially designed to meet Voltavision's requirements. It is the first in a battery testing laboratory to be operated with propane. With a GWP of less than 3, propane is very environmentally friendly. By comparison, other common refrigerants such as R449a have values of 1,397.
Propane has some special requirements that are easy to control, especially with centralized refrigeration. Voltavision has therefore developed a central refrigeration system that is operated with an evaporation temperature of -23 °C. The system cools an ethylene glycol to a permanent -15 °C, which has a frost resistance of -45 °C. The cold water-glycol is pumped through the laboratory via a large ring line.
Cooling in the central refrigeration system is provided by two redundant compressor units, each with five compressors. The redundancy ensures reliability in the event of technical faults, but can also be used to supplement capacity. The output of the combined system is controlled as required by an MSR system developed in-house.
Voltacooler with CO2 booster set for low temperatures
In the Voltavision Riemke III laboratory, the glycol from the central cooling system cools the Voltacooler integrated into the test chamber and the test room directly via large heat exchangers. This means that each test chamber can generate temperatures down to -10 °C directly via the central cooling system without an additional cooling circuit, which requires significantly less energy than conventional systems. The use of a CO2 booster then ensures a temperature reduction down to -40 °C within the chamber and the cooling circuits for the test specimens. The Voltacoolers have been adapted accordingly so that they can also be operated with CO2 as a refrigerant. The Voltacoolers, which are infinitely variable from 0 kW to 20 kW, and the CO2 boosters are installed in a compact frame. With a footprint of just 90 x 120 cm, a particularly compact design has been achieved that is based on the dimensions of the previous Voltacooler.
Propane chiller provides further optimization
The central refrigeration system is supplemented with an additional chiller, which provides a glycol temperature of +20 °C at 100 kW and primarily cools the output stages of the battery testers. It has a free cooler so that the glycol is cooled via the environment to save as much energy as possible. The system is also connected to the new Voltacooler with CO2 booster to act as a desuperheater stage for the CO2. The chiller cools the battery testers with a high proportion of free cooling and also ensures energy optimization of the CO2 systems.
In the course of the Riemke III laboratory construction, the cooling of the Riemke I and II laboratories will also be modernized in order to make the entire refrigeration production more efficient and to drive forward the complete conversion of the operation to natural air conditioning agents. Both laboratories will be equipped with KWS with free cooling, including the use of the environmentally friendly refrigerant R290 (propane), so that they are cooled efficiently and in a climate-neutral way.
Would you like to find out more about our climate-neutral refrigeration technology?
Or would you like to report on our climate-neutral refrigeration technology in your (trade) magazine? Then I look forward to hearing from you.
Katrin Ruff
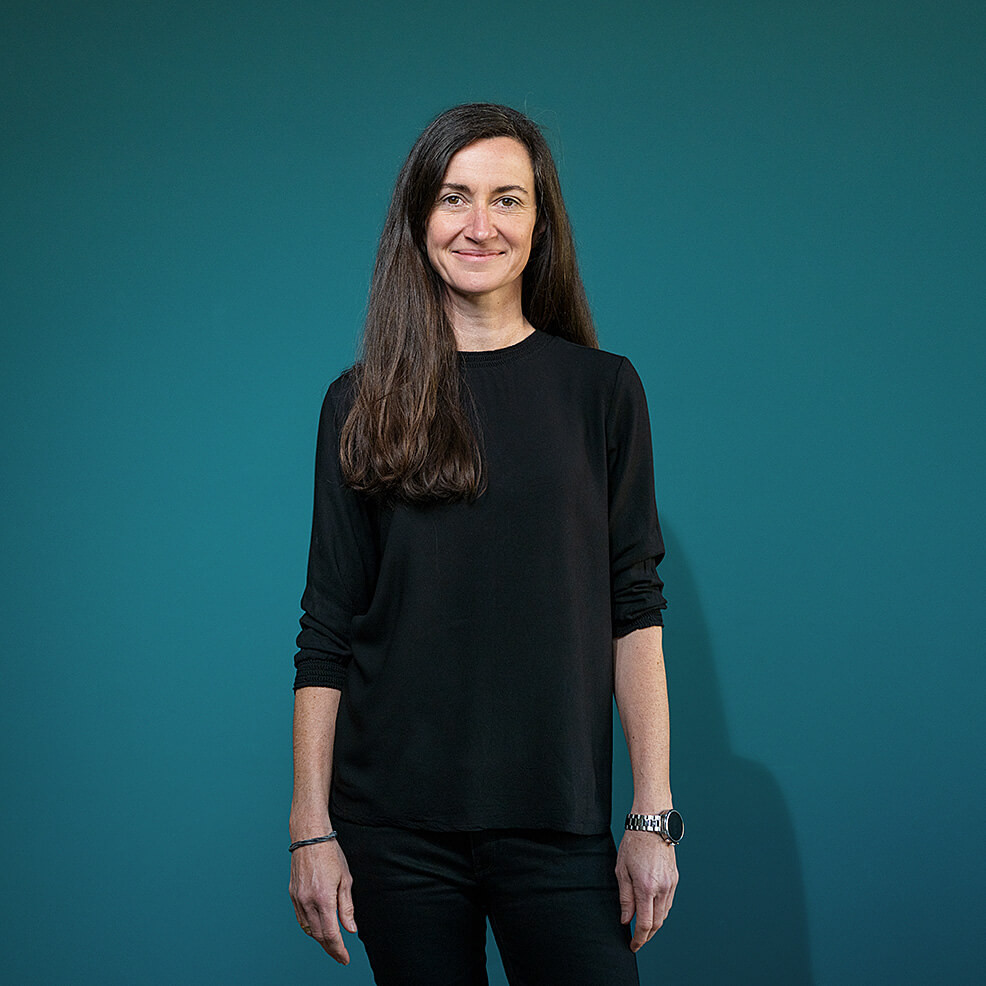
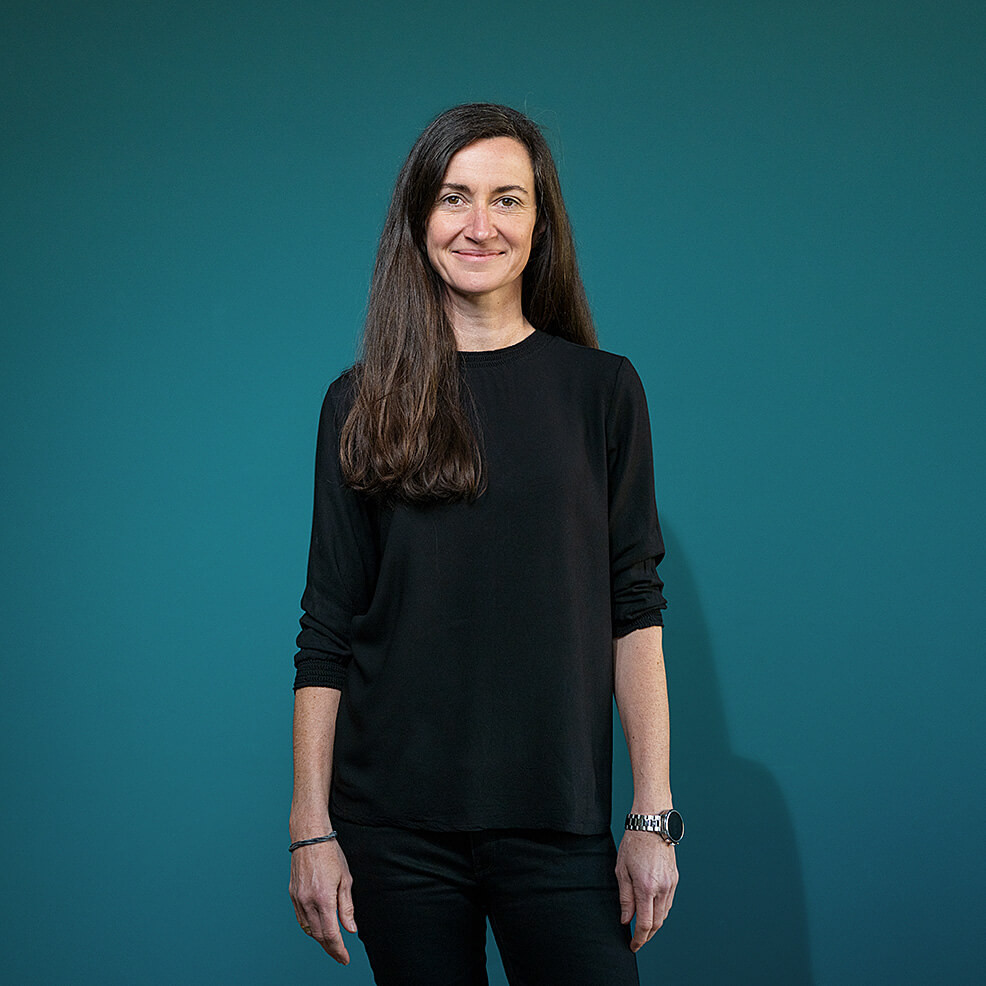